After the construction and during use of the Dinofort project, one of the floors broke underneath about 40 dancing students. It was a terrifying moment as an engineer to see something I built fail, in a way that could hurt people. Luckily none of the dancers noticed, and the floor only caved in 3 inches before it touched the ground, but nonetheless our hard work had still failed in customer use.
That prompted the need for further investigation. I spent the next semester conducting research and writing a research paper, poster, and several oral presentations on the topic to better understand the mechanics that could have caused the floor to fall. More importantly, I wanted to see from the data if changing some simple parameters of how it was built could lead to better results.
Over the fall of 2016, I built models of butt joints and subjected them to a range of cyclic forces to mimic the conditions the fort floor felt during the party where it failed. I ran my experiments on an Insteon, collected data and interpreted all results in the Matlab software suite.
While I did not find any conclusive results, I am happy to have conducted a long-form research project to see if simple (cheap) solutions could measurable improve results for the following years attempts at building forts. While I didn't conclude anything from my research I then put together a list of possible other fixes and presented those to the next year's fort team with hopes that they implement them.
Here's a look at the project as a whole, starting with a close up (one of the only photos we took that night the floor fell !) of the sheared / pulled-out screws.

Here is the poster I made on the subject showing the results of my research. I also wrote a research paper on the subject documenting my experiments, methods and results; if you are interested I can send it to you!
Either way, I highly suggest reading The Wood Handbook.
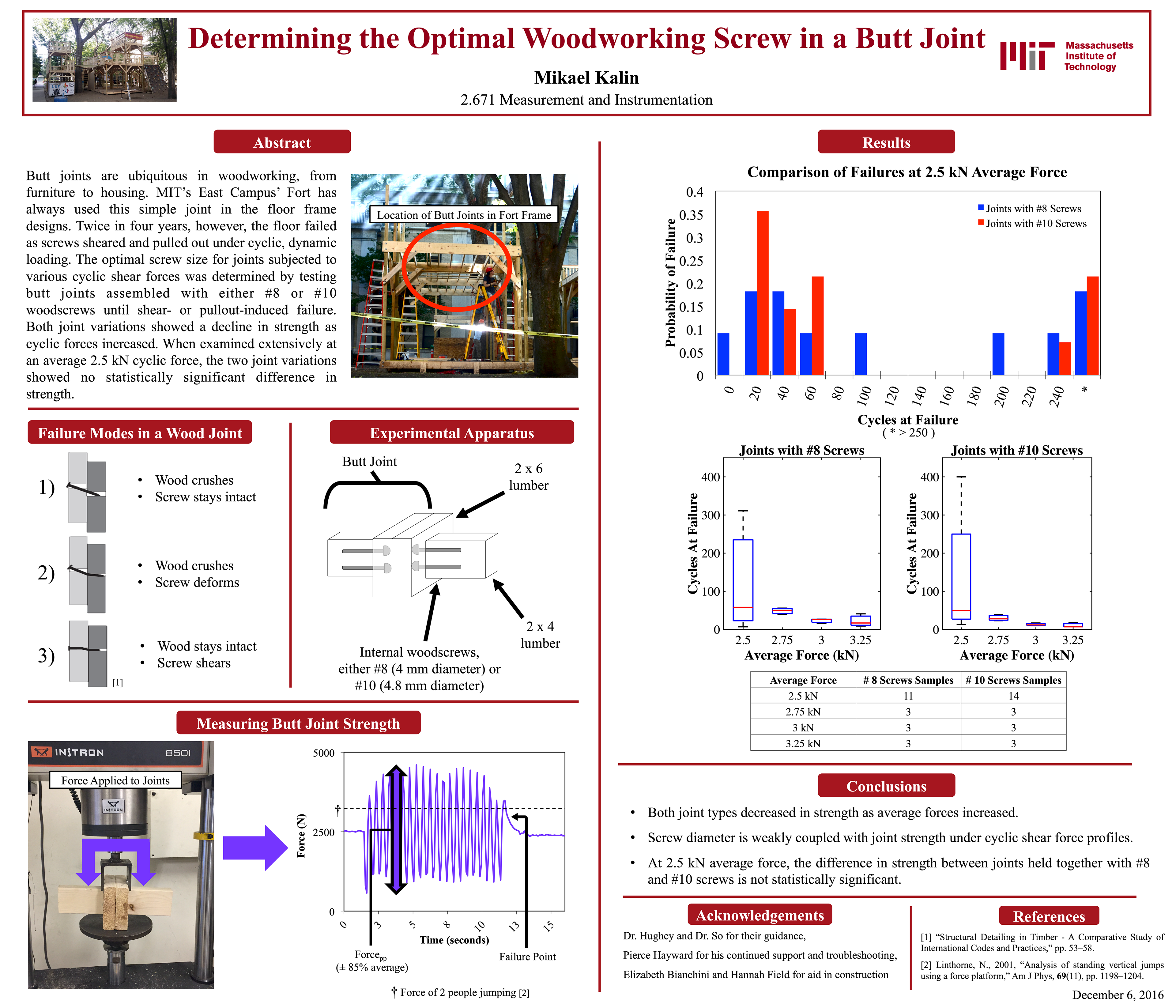
The instron set-up I used. And then close-ups of the "failed" joints, showing both screw shear and pull-out.
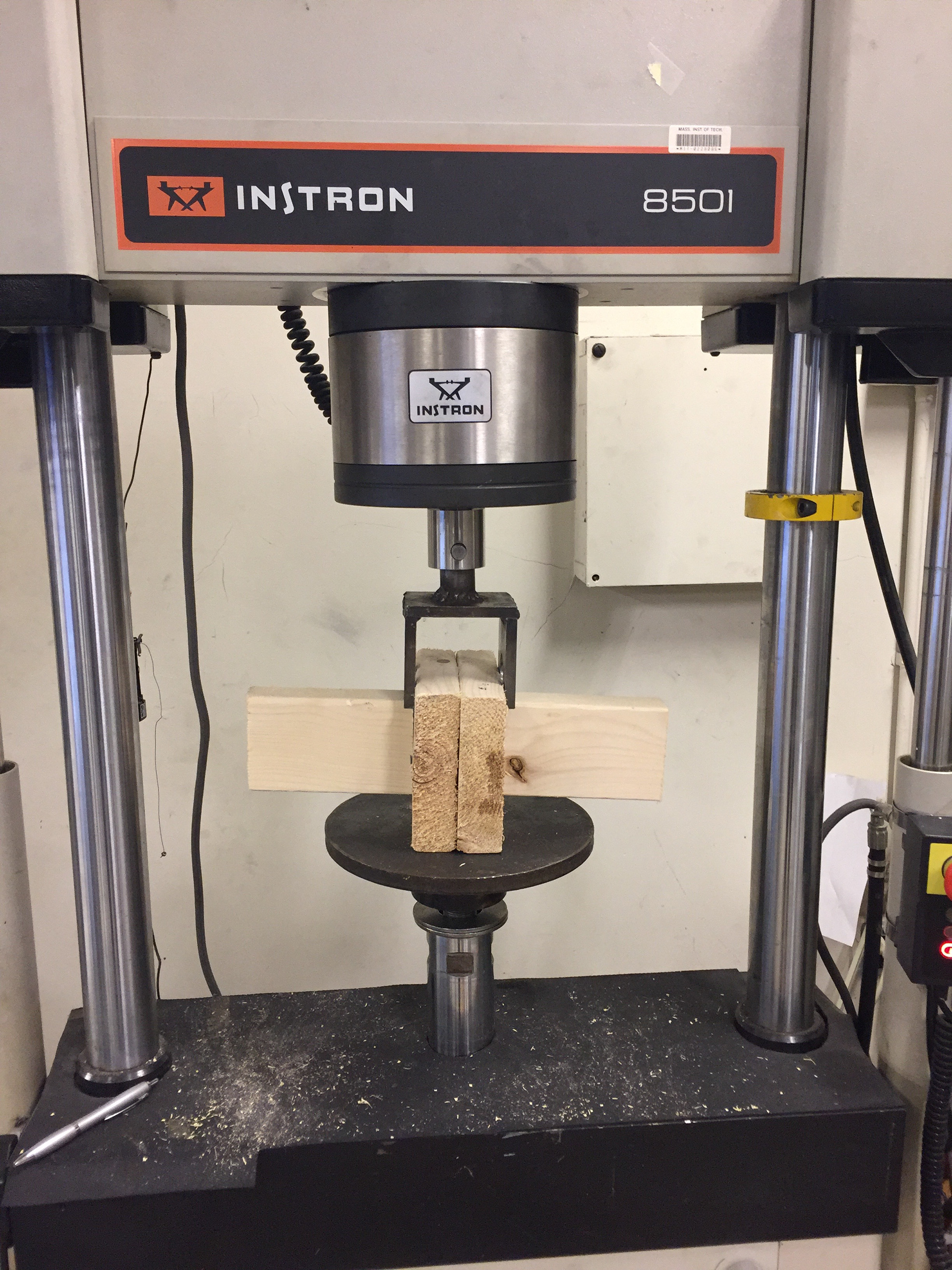

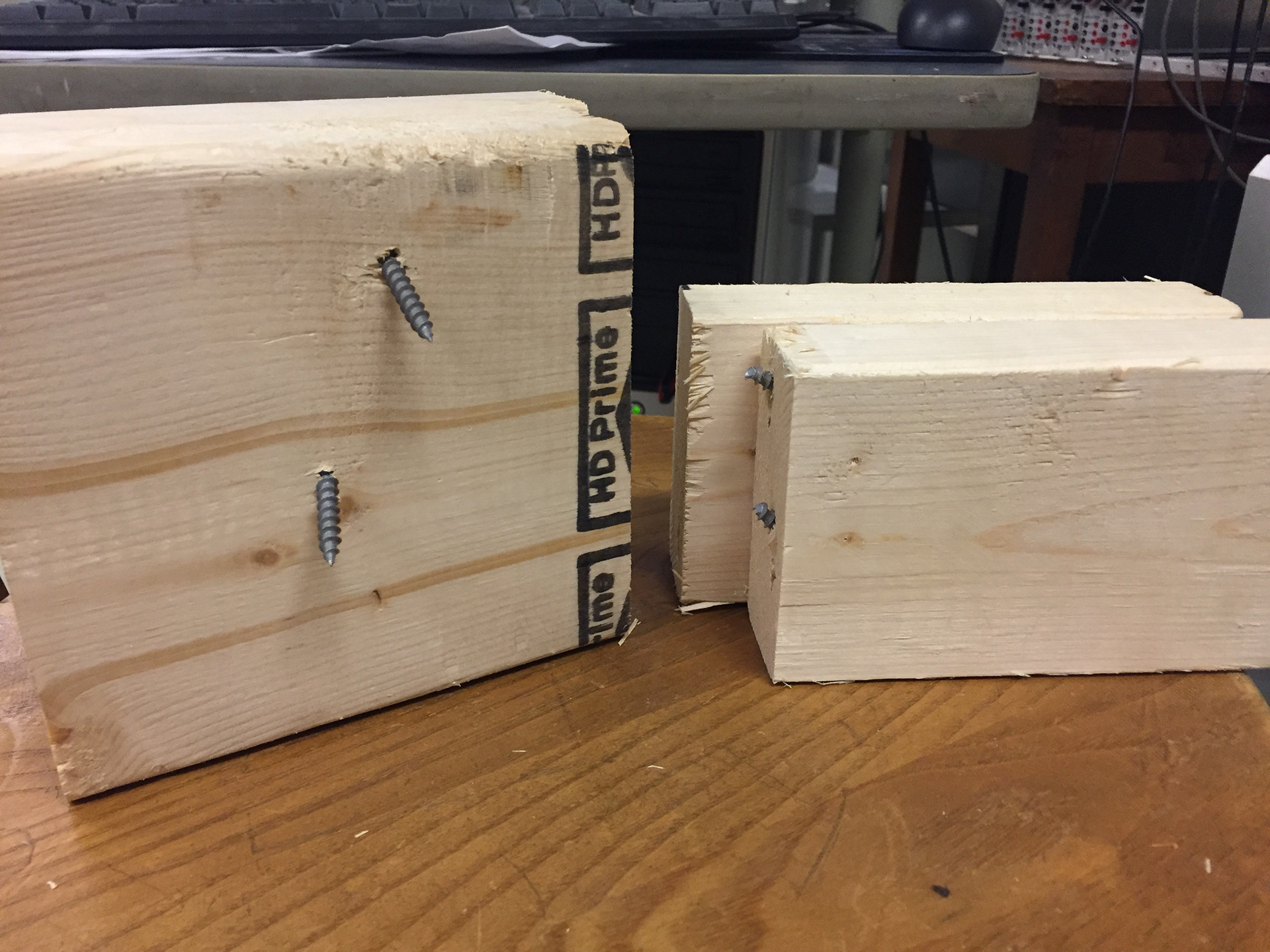