As part of my Design and Manufacturing II class at MIT, I made 60+ functioning yo-yo's in a team of 6.
Over the course of three months, I designed (drew) designed (CAD'ed) parts for injection molding and thermoforming. I designed aluminum and 3D-printed molds, wrote G-code, and oversaw the manufacture of 1/3 of the yo-yo's shown below. During manufacturing, I recorded and analyzed machine parameters to create control charts and monitor runs to meet critical dimensions for press fits and snap fits.
Our yo-yo was the best in the class (if I can say so humbly), and it was one of the most technically challenging ones this class had seen in its 25+ year long tradition of yo-yo manufacture.
Overall, our team shot and thermoformed over 1,000 plastic pieces to create and assemble 60+ identical, functional, and quality Murakami yo-yo's.
See below for the process and some fun pictures of my machine work.
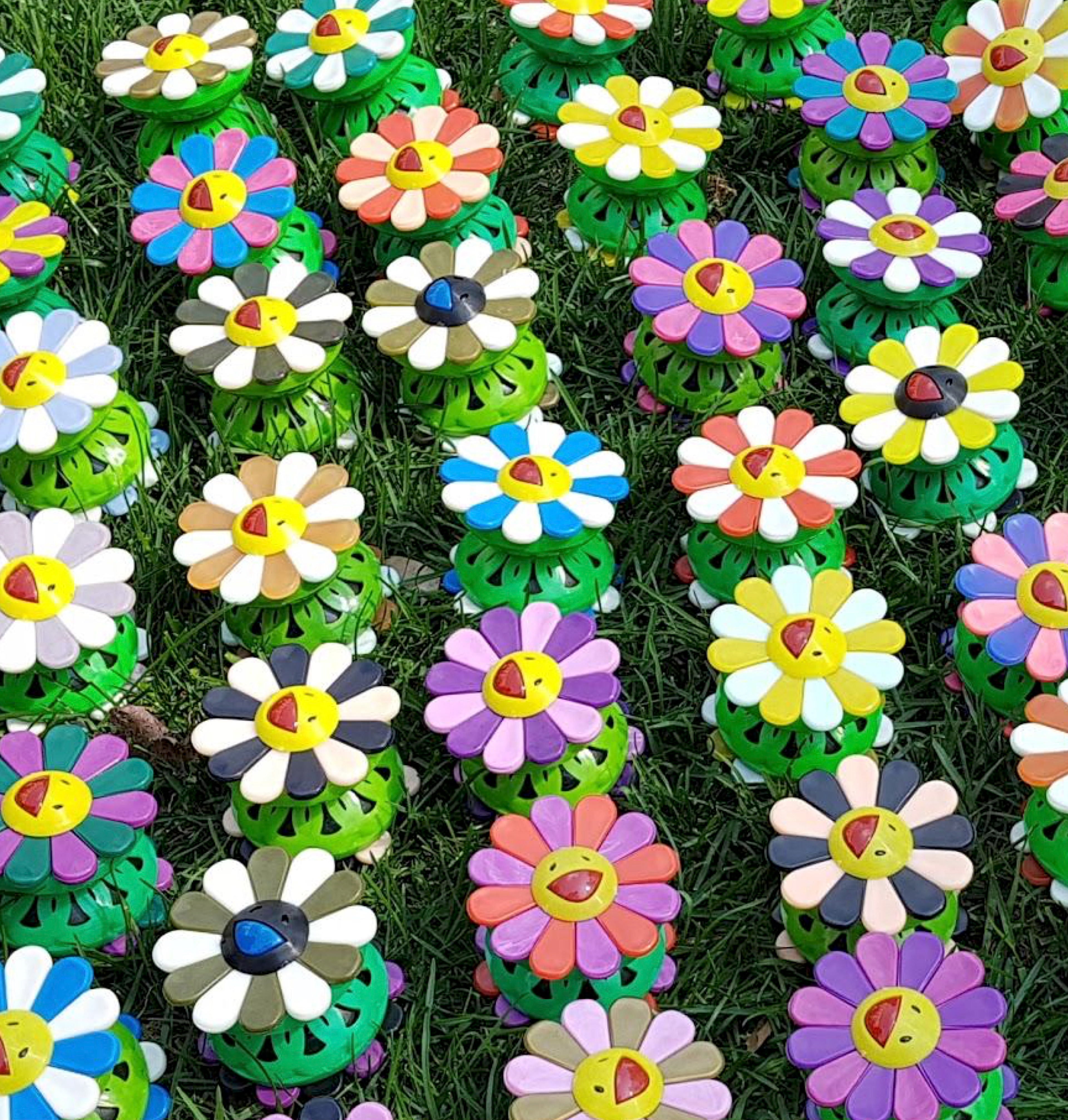
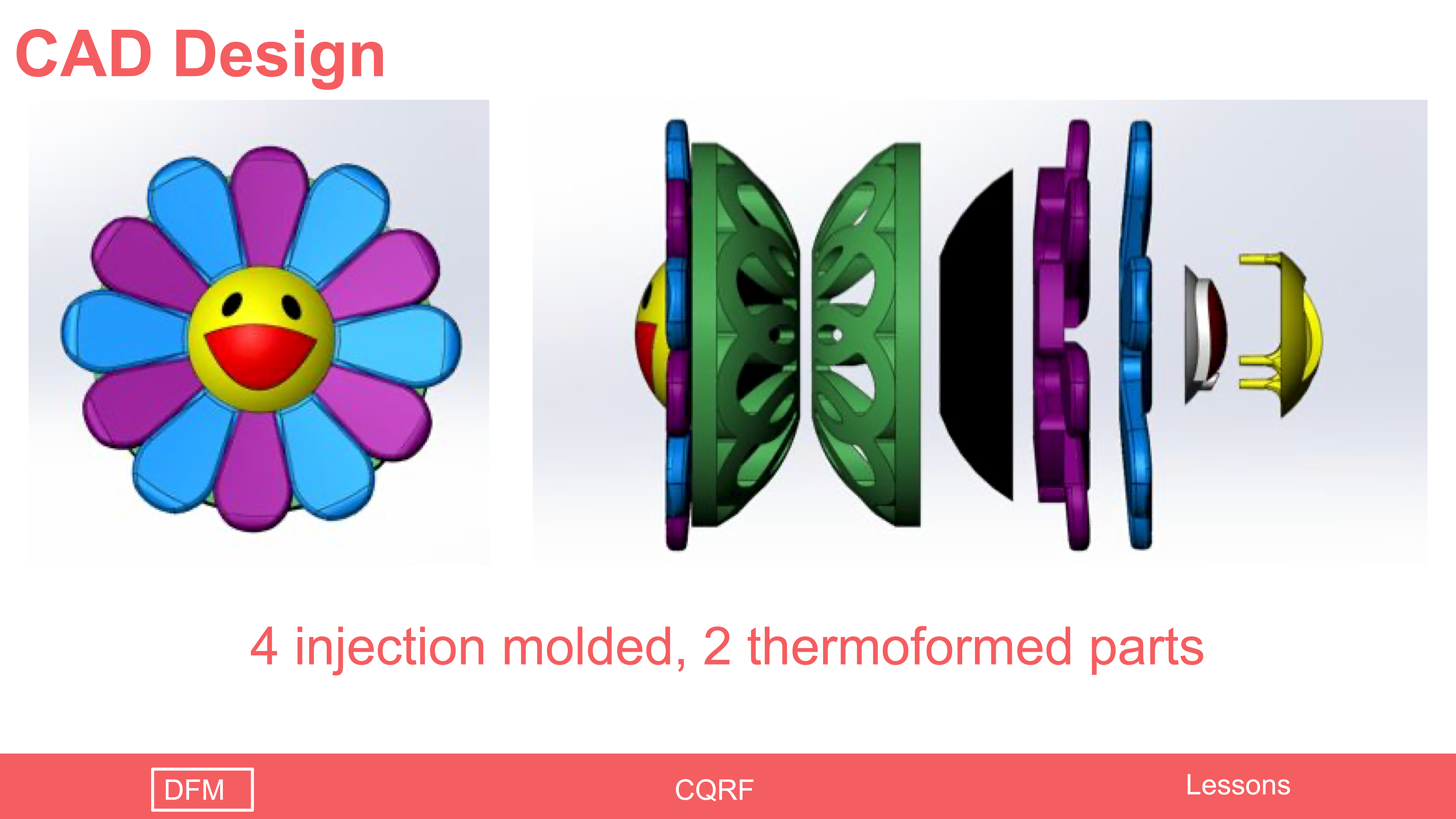
Below is a sample of the drawings I made for the thermoformed part, the injection molded part, and the injection mold itself.
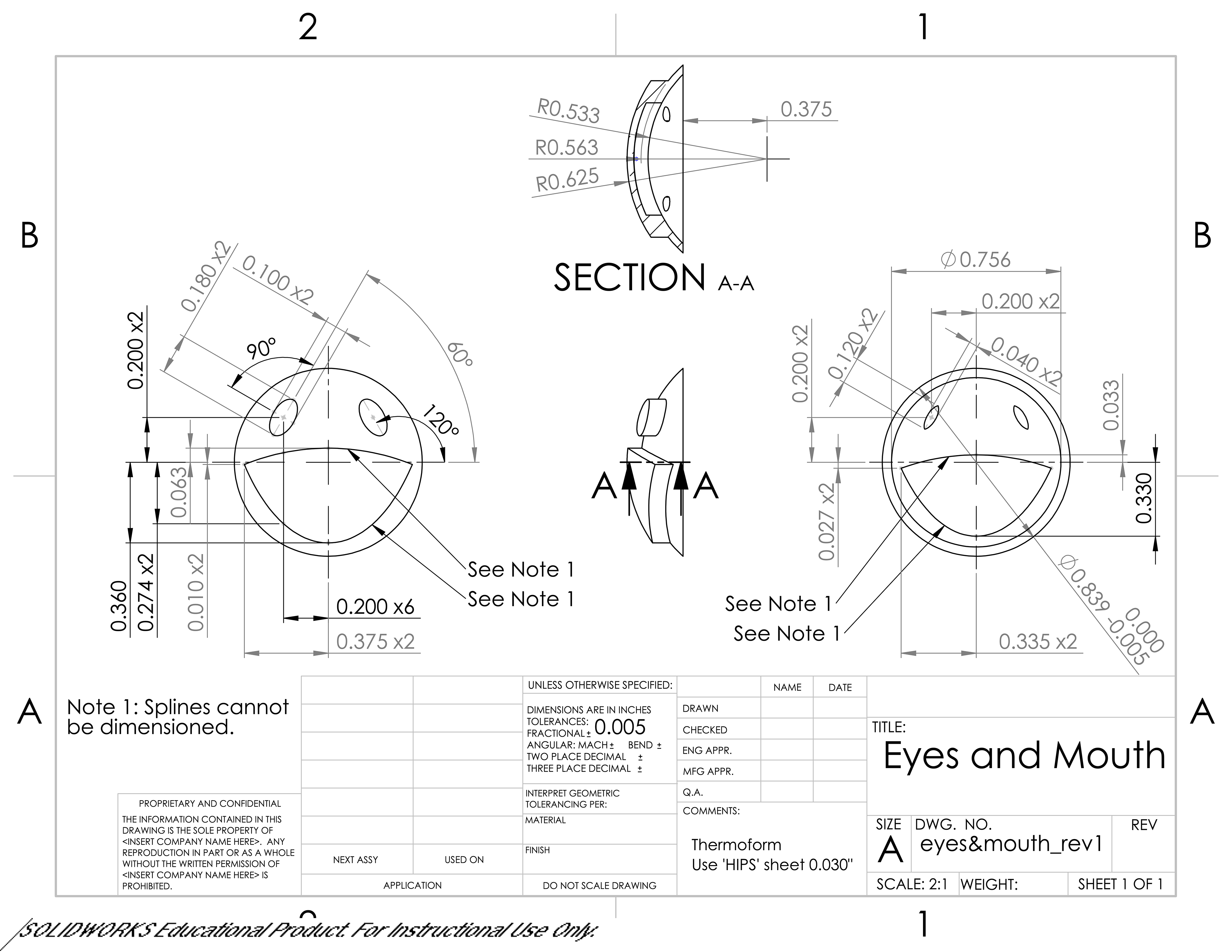
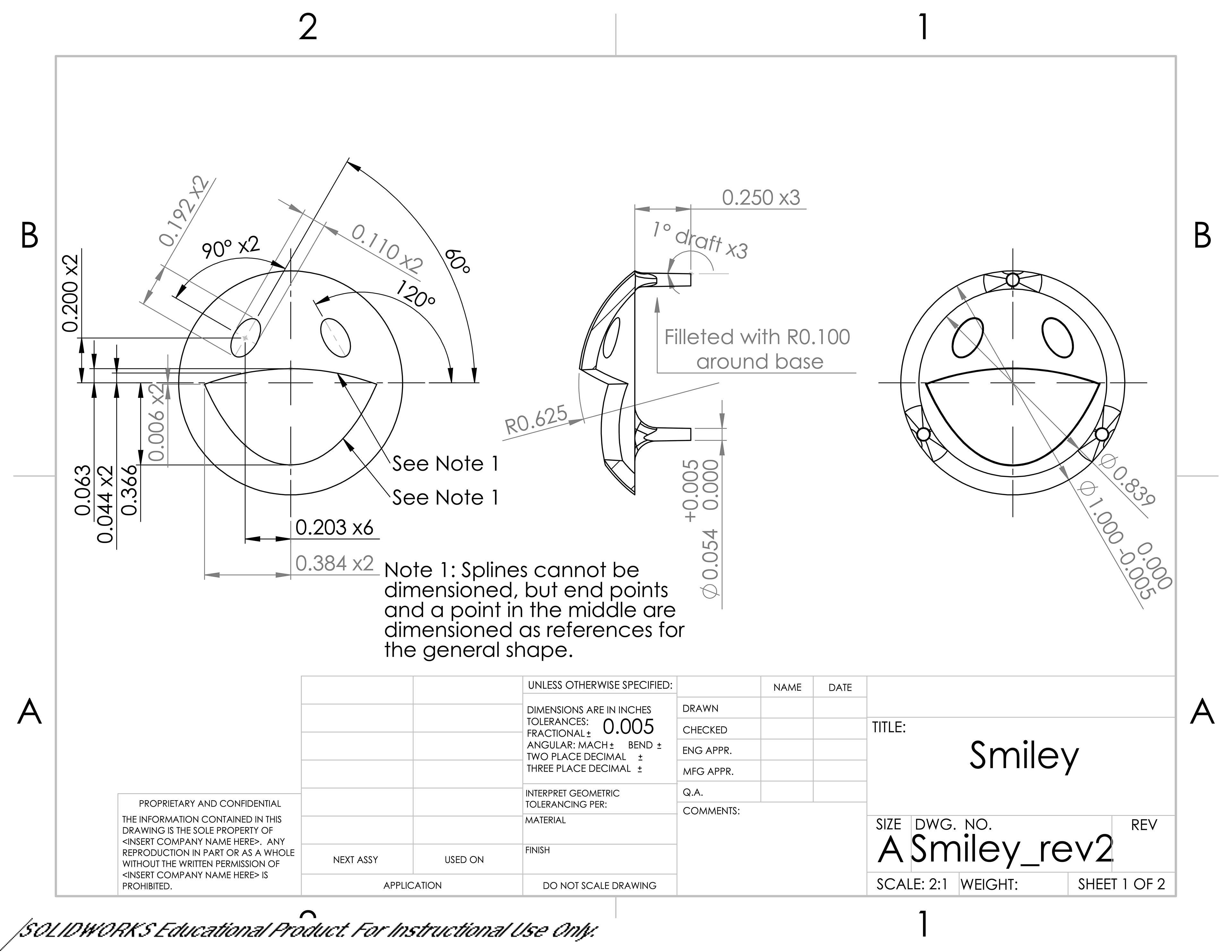

Here are the aluminum molds! Of the ones shown, I was in charge of the bottom left one, but helped machine and CAM the others as my teammates asked.
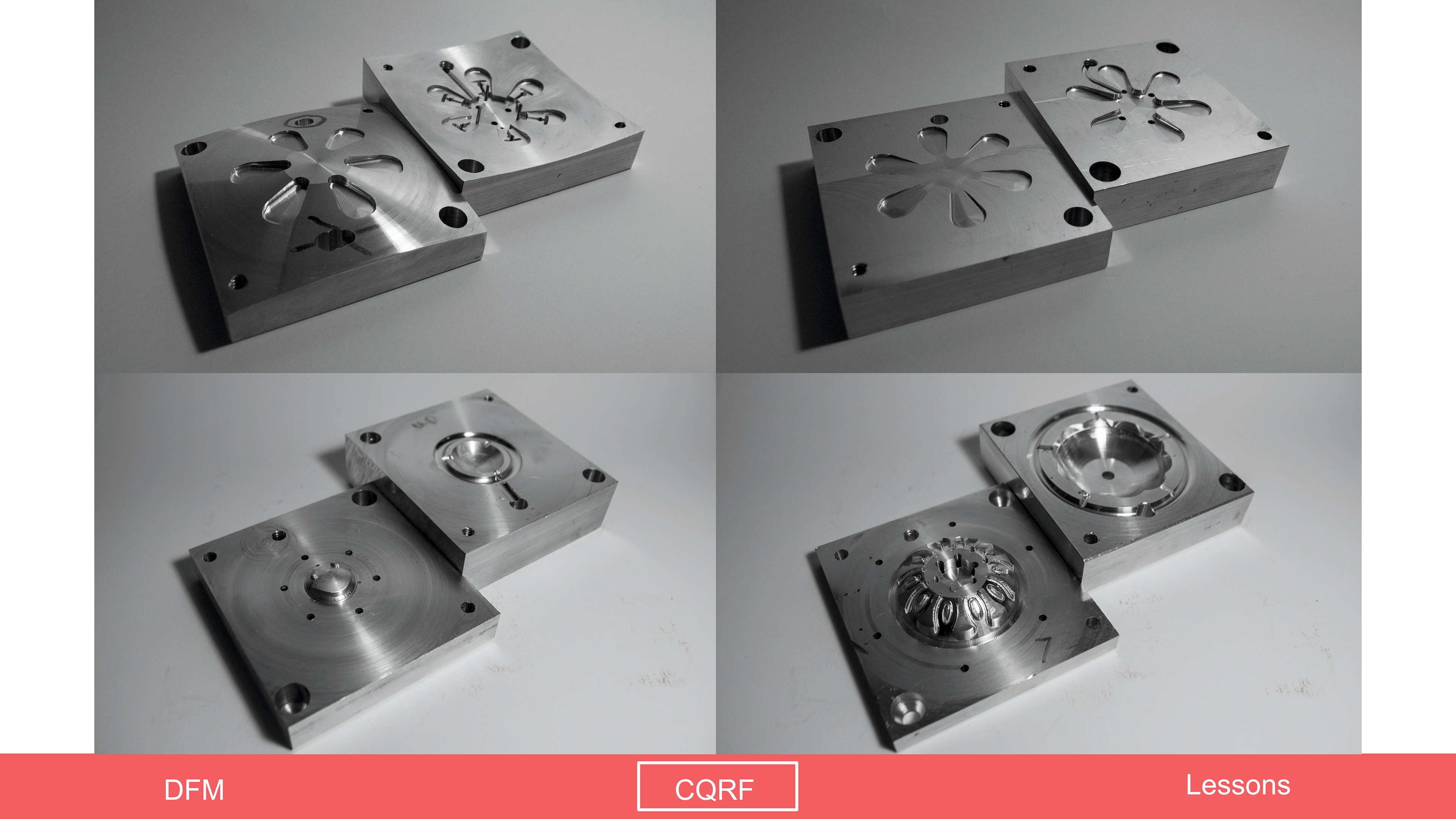
Throughout the process, we were aiming to get uniform and perfect parts. Here you can see my final part and the mold that made it. I had a few short shots in the beginning and parts with flash as I learned to tune parameters of the machine. I had to rework the mold twice because the part was not being properly ejected. In the end, after remaking molds and polishing countless times, it took some mold release spray and the parts were literally flying out of the machine. If only I had sprayed the first time!
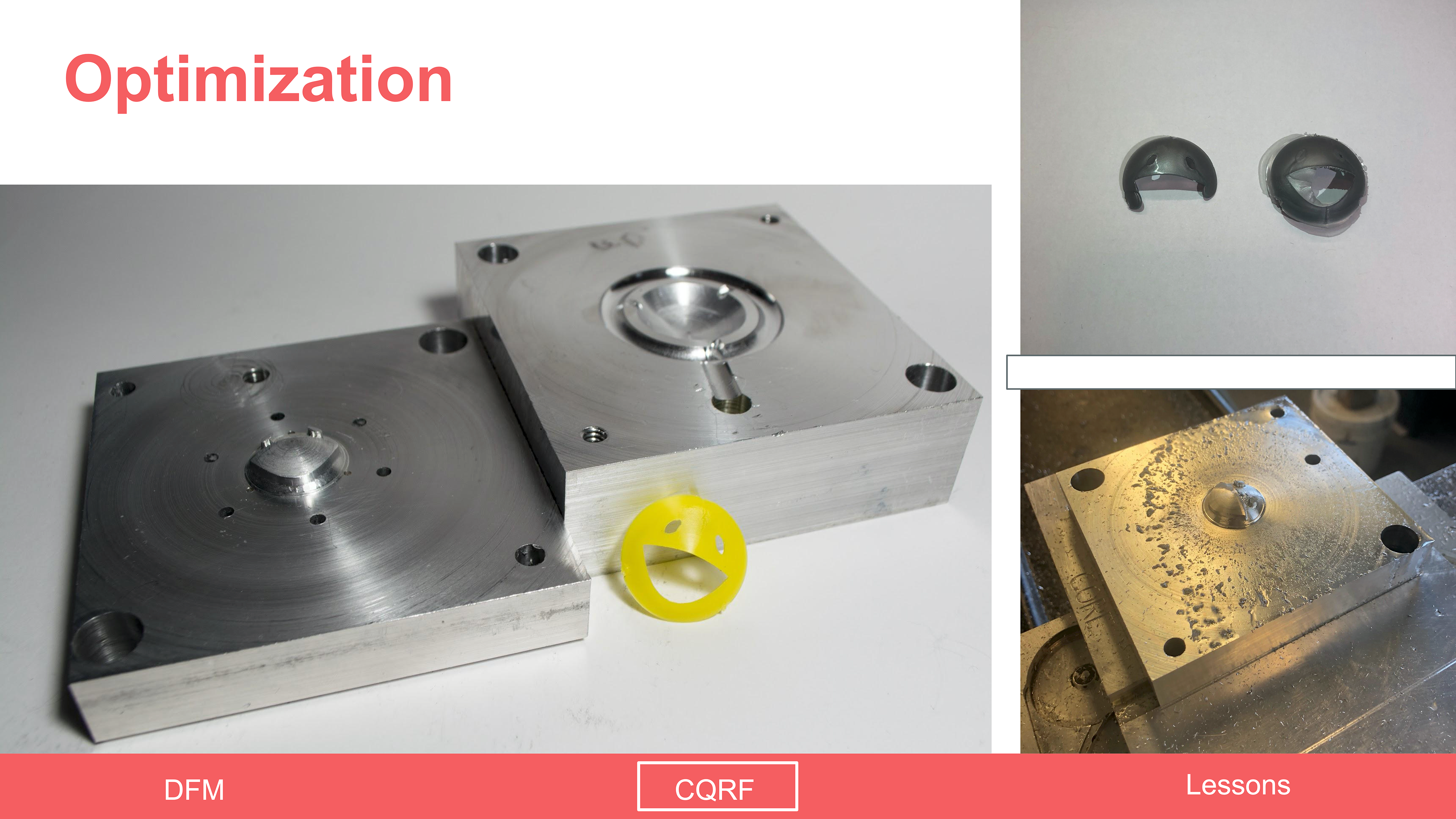
The small gallery below is a sample of the control charts, x-bar charts, run rates, and cp / cpp calculations for the parts. I changed some parameters, and could show how changing temperature of thermoforming heat applies changed results, or how decreasing cooling time had dramatic effects on the parts.

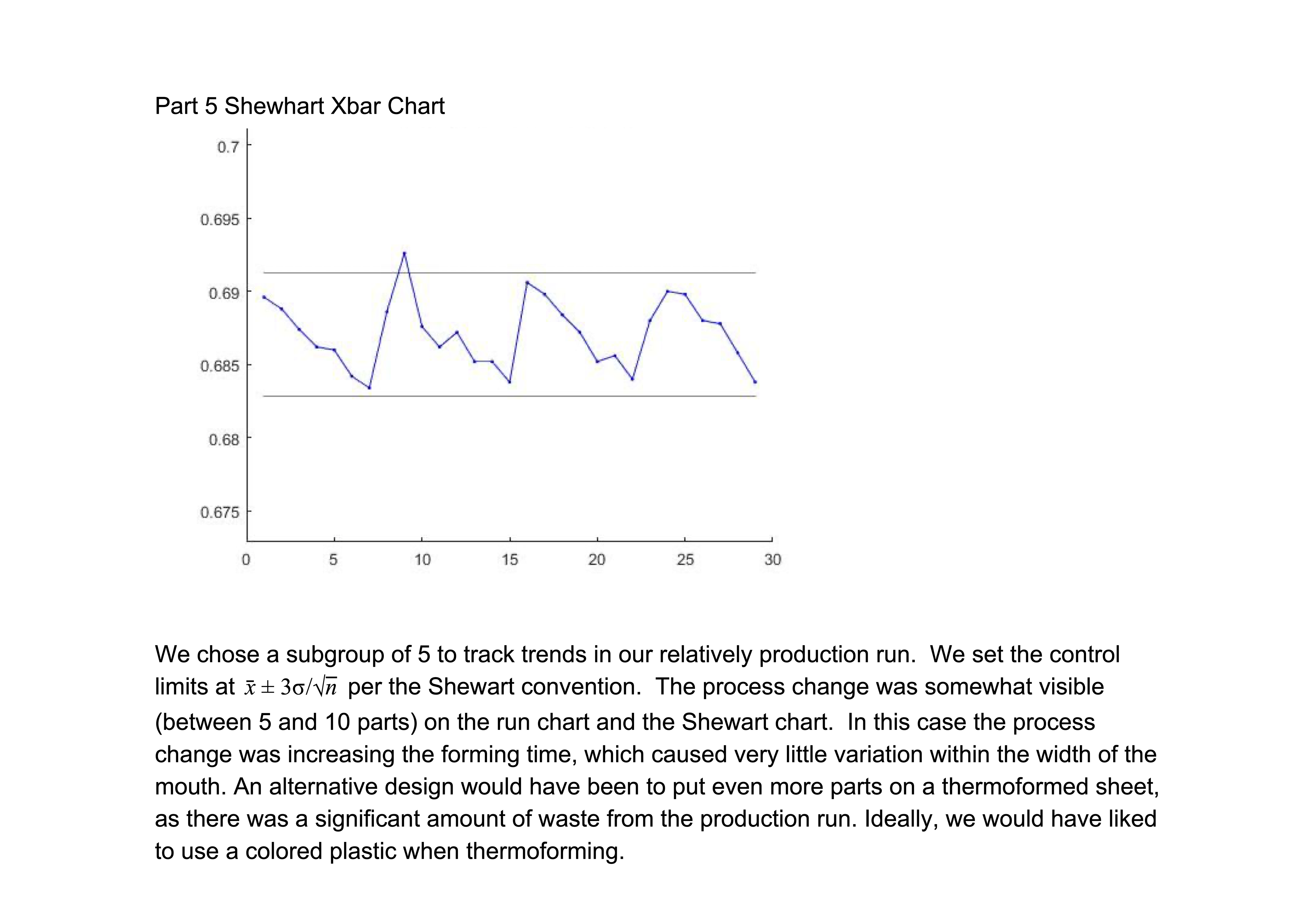
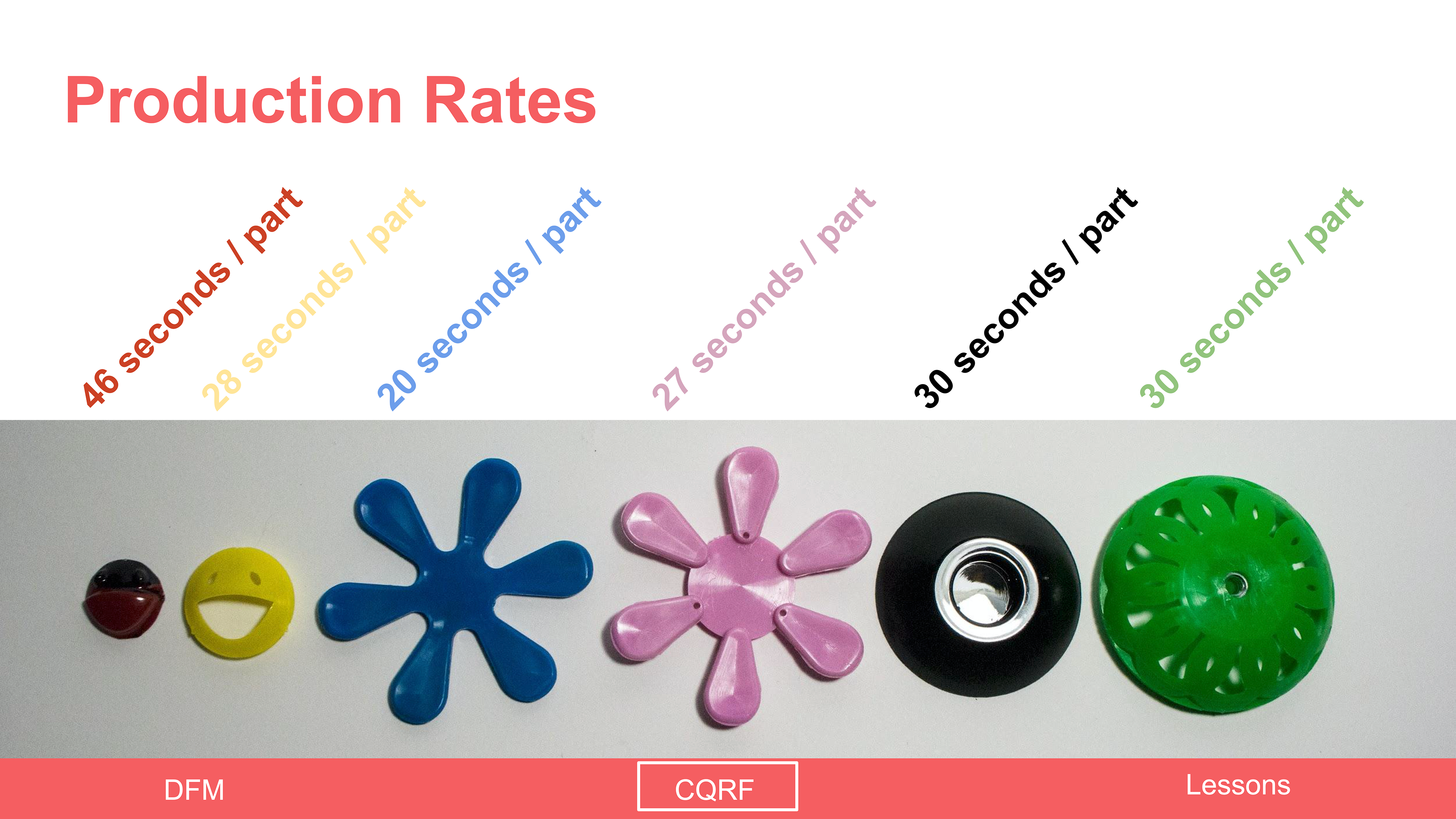
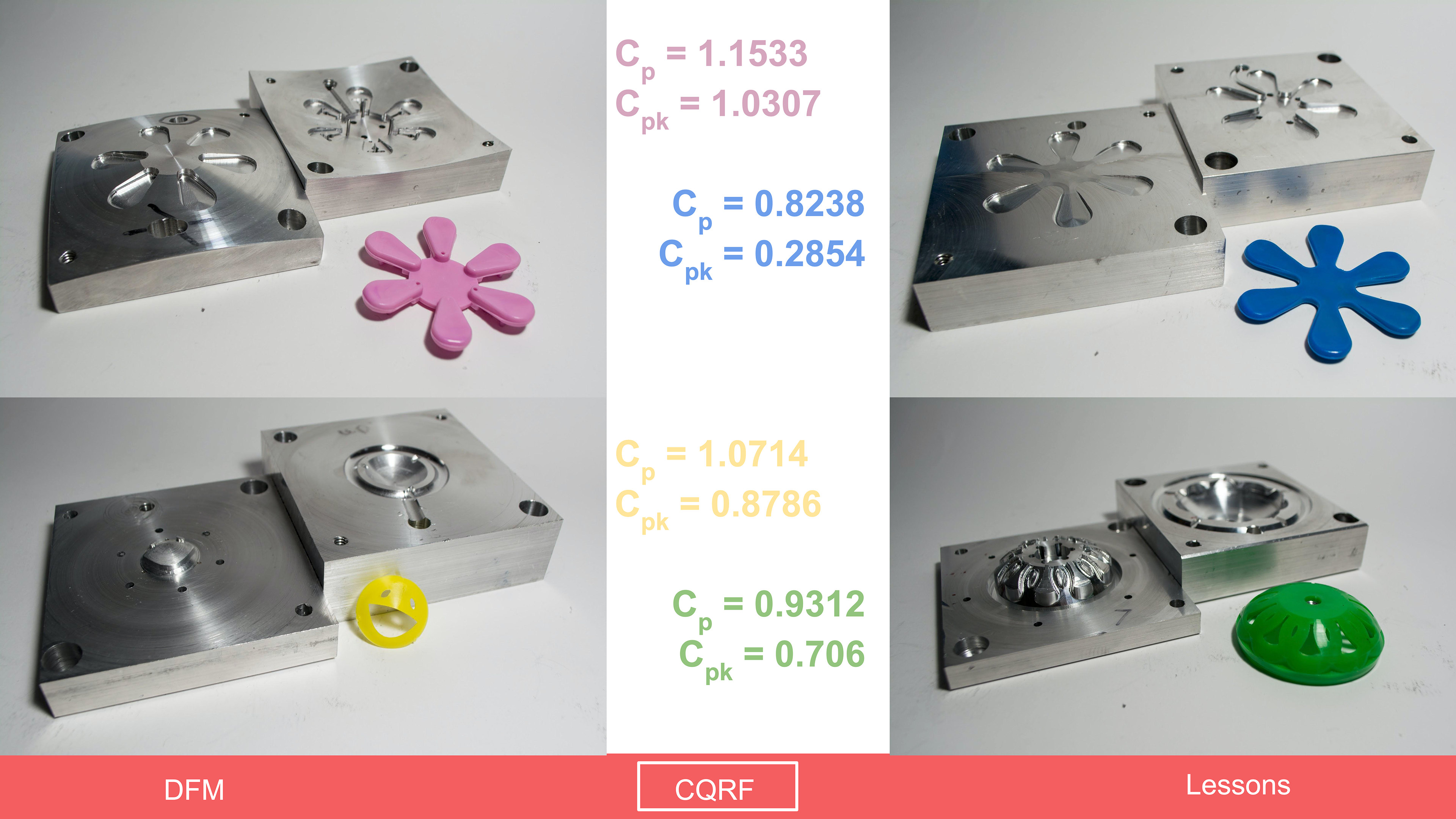
The absolute best part of this entire process was working with my team! We had 6 highly motivated, extremely talented engineers. We'd regularly be the first people in the lab getting there before it opened at 6:30 to get our work done early. We became friends with the shop staff, and were helping other students run the CNC's. In the end, we were completely done with shots and assembly an entire week early on our 11 week timeline from ideation to turn-in. It was an incredibly successful project, and we all learned a lot.
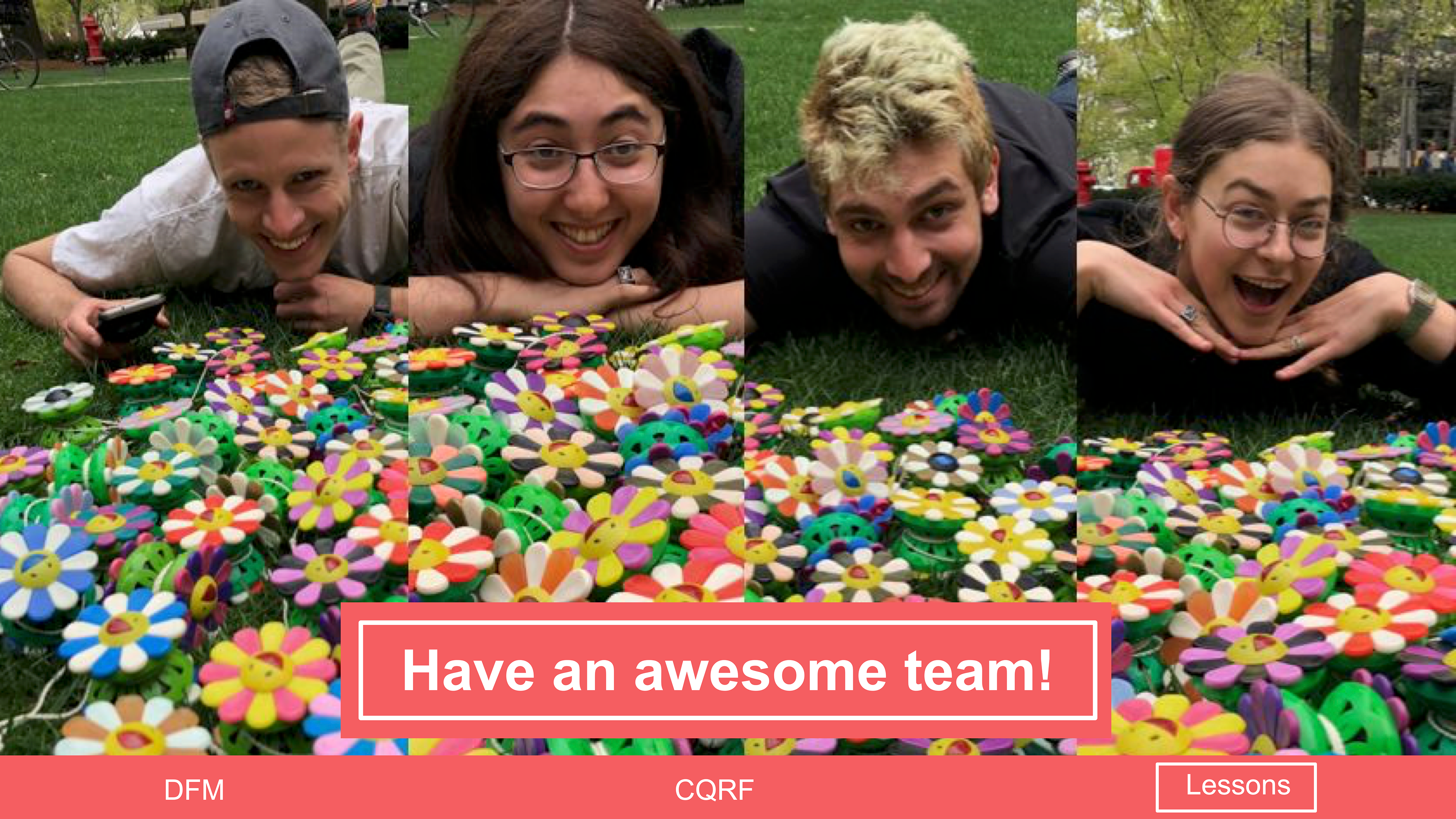